|
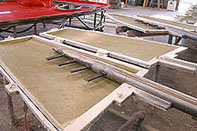
Rudder mold with a tapered stainless
steel shaft in position for the foaming process.
|
The construction of our
rudders has changed considerably through the years in order to improve
strength, durability, and reliance. The closed cell foam
core of the rudder has remained the same. But the
selective
addition
of
unidirectional fibers has increased the strength of our rudders,
and the use of Vinylester™ resins has eliminated blisters and
the need
for
expensive
barrier
coats. All of our Foss Foam rudders come
sanded and ready for bottom paint, and they can be shipped anywhere
in the
world.
If
necessary, we have the capability to use a special "vacuum
bag" production
process to create especially strong rudders. We can also use core
materials of various densities, or use carbon fiber in order to construct
high performance parts and components. Here
is a closer look at how we manufacture our
most popular line of rudders:
Rudder Construction Process
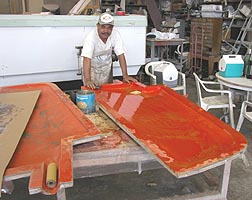
1. Our
employees begin the manufacturing process by sanding,
polishing and waxing the rudder mold.
|
|
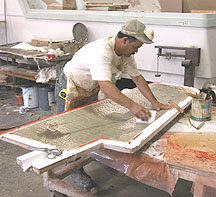
2. After applying Gelcoat to
the mold, they apply a layer of unidirectional fiberglass
saturated with Vinylester™ resin.
|
|
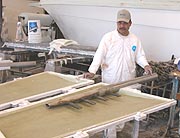
3. Once
the fiberglass has cured, they place
a tapered stainless steel shaft into the mold. Then
they
pour
liquid foam into the mold and clamp both halves together.
|
|
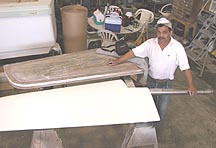
4. When the foam has cured, our
employees open the mold and remove the rudder in preparation
for final finishing.
|
|
|
|
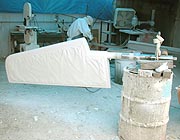
5. Next,
they sand the parting line seams of the
rudder, then apply fiberglass
and Gelcoat to the seams as well.
|
|
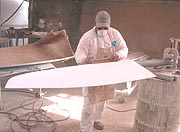
6. Finally,
they sand the entire rudder and prepare
it for the client's future
coat of
bottom paint.
|
|
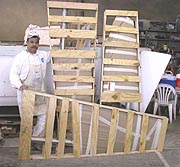
7. When
the rudder is finished, our employees carefully pack
it in a crate suitable for
shipping anywhere in the world.
|
|
For more information about our line of Foss Foam replacement
rudders, please call (949) 646-0244 or contact
us at our offices in Newport Beach, California.
|
|